COMPANY
NEWS
All developments will be shared with you here
R. A. Lister Petter – a personal look back
I came into the employment of R.A.Lister & Co. Ltd. by chance in 1969. I had committed the cardinal sin of failing a re-sit exam at the end of my second year degree course at the National College of Agricultural Engineering, Silsoe, and wished to spend the obligatory “time out” in gainful employment until repeating the exams. Living near Ross-on-Wye, RAL’s Cinderford factory was about thirty minutes drive from home. I decided to visit the works to try my luck with the Personnel Dept. I got no further than the Gate House in Barleycorn Road, where I was turned away by the Gate Man –
“We don’t take on temporary workers!”
Not at all put off, I returned home and rang Personnel, and was invited to come for interview with Mr. Ralph Mumford, the General Manager, that very afternoon! Arriving at the Gate House, the irate gate man said
“I thought that I told you to go away?”
“You did, but I have an interview with Mr. Mumford at 2.30!”
The interview went very favourably, and I was offered a job of assistant gen-set tester in the newly established Gen-set Erection Section, to start in two weeks time. Ralph Mumford kept a close interest in my employment until it was time to return to my interrupted studies. (I later learned that the gate man was the father-in-law of the General Manager!)
RAL Cinderford part-manufactured and assembled the slow speed CS range of Lister engines, and also produced many components for Dursley and Swindon. The Genset Erection Section worked with the LR 1-2 and SR1-2-3 engines produced in Swindon, together with a few 8/1, 16/2 and VA engines, to be coupled with either BKB, EEC or Brush alternators. Bespoke control panels were made in house.
(In passing, the VA was effectively an air cooled single cylinder version of the 8/1, with different timing, bmep and sfc – somewhat noisy!)
The RAL factory in Cinderford employed many displaced coal miners from the Forest of Dean coalfield, who had endured great hardships and very low wages. Highly skilled former pit electricians found welcome employment when RAL moved the SR gen-set production from Walkden or Swindon to Cinderford, supplementing existing 8/1 and 16/2 (plus the very occasional VA) gen-sets.
Once familiarised with the team and trained on the engines and equipment, I settled into the tasks of receiving the built-up gen-sets and the separate control panels, wiring the two together and connecting to the load banks, connecting up the exhaust, batteries and the fuel supply. All engines had previously been tested and were ready for full-load, but all of the wired-up panel components were unadjusted. I progressed from testing simple battery charging sets through stand-alone single phase and three phase, then on to Start-O-Matic, marginal mains failure, dual stand-by, auto-standby to mains, marine auxiliary sets and long-running sets.
One of the first tasks was to adjust a host of relays of the control panel (this being before the age of solid state electronics) with a Variac and an AVO meter. I made myself a small stool to facilitate working on some of the panels too big for wall mounting, as the adjustments were time consuming for the more complex sets, typically taking half a day if there were any novel features in the wiring that caught the Panel Section unawares. Next the engine controls had to be set – the Low Oil Pressure and the High Air Temperature cut-outs. The engine could then be started (and the logic sequence monitored in the case of engines with Start-O-Matic fitted and dual systems), run up to speed and operating temperature, and no-load voltages checked and specified resistive loads applied, and battery charging rates set. If all went well, the shutdown procedure was monitored; in the case of dual sets, the start-up of the second set had to be similarly monitored, and the full test then applied. None of the sets were arranged to be run in parallel.
As a general rule, the alternators fitted were either Brush or BKB (the latter, made by Bulpitt, Kent and Bulpitt of Birmingham, were being phased out as the Hawker Siddeley Group in-house purchasing policy took hold). In earlier days the alternators and generators would have been made by Mawdsleys of Dursley.
For most customers, the RAL-conducted tests were sufficient proof of performance. However, institutional customers, typically Lloyds, Crown Agents, Westinghouse and Philips with critical fail-safe systems, invariably sent their own inspectors to observe “Witnessed Tests”. It fell progressively to my lot to conduct such tests, of greater or lesser complexity, including the first dual standby long running SR1 generating sets de-rated for high altitude for the new East African Microwave telephone links being installed by Philips bv. Some of the Lloyds sets were marine auxiliary units incorporating a mix of alternator, air compressor and fire/bilge pump! (Not all used at the same time – in-out clutches and lock-out switches enabled some selection of functions). Crown Agents orders included some airport gen-sets arranged for dual standby to mains, progressively falling in power such that the final generating set powered only radio beacons and the rudiments of air traffic control.
In the six months that I was involved with the Gen-set Erection Section, we never had a single test failure. I did however condemn a whole pallet of Lucas regulators, and had to instruct the Panel Section in the importance of observing the polarity of high current diodes (their first solid state device, introduced in 1969 for SR1 battery charging sets).
Considering that the most complex of combinations involved two switch panels each the size of a small wardrobe, the respective Sections performed some remarkable feats working at “arms length” from the design team. On only one occasion did we have to call the Chief Electrical Designer over from Dursley to interpret the logic sequence in the Specifications. I well recall the occurrence, as Harry Taylor arrived just as I was about to clock off: I earned an extra 5/- for the resulting short period of overtime, but paid an extra 7/6d in tax that week, (having crossed a tax threshold)!
My duties were never clearly spelled out, as I was effectively on trial, being the best technically educated person in the Gen-set Erection Section. Only two months after being taken on, my foreman Ray went on extended sick leave after a hernia operation. I soon found myself having to deal with admin and technical problems which the other foremen were reluctant to take on, and learned a great deal about management as a result.
The gen-set market was buoyant, resulting in a hive of activity: this, coupled to a boom time for slow-speed engine production, meant everyone was on bonus during early 1969.We willingly worked
- A five day week
- Overtime three evenings a week (Monday, Tuesday, Thursday)
- Half days on Saturdays
- All day on Sundays
And not a single complaint! My pay as a gen-set tester (with overtime and bonus, before tax but after deduction of weekly blue overall costs, NI contribution, etc.) was £25 per week. The tax was recovered once I returned to my studies.
Whilst devoting most of my time to my testing duties, I took every opportunity to observe what the factory did and how it was managed. A wide range of engine and other parts were being manufactured on machine tools common to all engineering works – Ward Capstans, Bar Autos, Multi-spindle drilling machines, Jackman grinders, etc. with a few more specific leviathans thrown in, such as Bullards. and Webster and Bennet vertical lathes for machining the twin flywheels that characterised the slow speed engine range. The pride of the show was the SocieteˊGenevoise jig borer for the Tool Room. There were other non-engine components and equipment being produced, principally agricultural machinery for the associated firm of Lister Agriculture. The HR4-powered Lister Moisture Extraction Unit (either skid mounted or trailer mounted) for crop drying, and the two models of farm feed pelleting presses were part-manufactured and assembled/tested in Cinderford, often competing for scarce labour inputs and machine resources.
The Genset Erection Section occupied part of a typical bay of a North-Light type factory unit, built in part from Government surplus materials in the post-war years., including from a wartime aircraft hangar in Windsor Great Park which had been constructed there in case the Royal Family were forced to flee the country. Rather over-specified steel columns supporting the overhead cranes had once formed part of the Mulberry Harbour! The bay was shared with the Packing Section, and was adjacent to the slow speed engine assembly and test bays. Parts stores were sandwiched between the component manufacturing and the tracks, with sub-assembly cells feeding in to the track at appropriate points.
As the slow speed engine components were of relatively ancient design, it was interesting to see how earlier manufacturing techniques were perpetuated. Typical was the camshaft assembly, where individual cams were heated and pressed and pinned onto a plain shaft. The crankshaft pinion was traditionally heated on a gas fired hot plate prior to being swiftly driven on – only in mid-1969 was an induction heater introduced. Many of the components were heavy, and called for muscle power to handle them. Although air hoists were in use to lift the flywheels, driving them on to the parallel crankshaft and fitting the gib-headed keys was hard work, sometimes needing refitting several times if the bore of the flywheel was on the tight side.
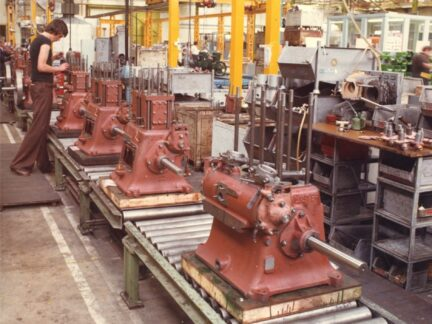
Looking at the picture of the Cinderford assembly line, a batch of 16/2 engines is in progress. Unfortunately no lifting hoist is shown for the separate cylinder barrels, which would be well beyond the capability of the lad shown! Where have all of the rest of the team gone? No doubt stood aside in the interests of clarity.
The orientation of the track and other features of the Assembly Section as shown differ from that prevailing in 1969, when I was employed on the adjacent generating set assembly and test; additionally everything is lighter and less Dickensian. The original spray booth (an Andrea Filter Back) may have been replaced – the paper type filter media was prone to catching fire. Unfortunately there are no sub-assembly operations shown – these were always peripheral to the track to feed in the assembled components at the correct stage, with the operators multi-tasking.
In 1969, there was a parts store with large stilages (looked after by “Herman Sid”) to the right of the track: a favourite trick was to a throw large Whitworth nut across the shop from the Genset Assembly Section on the left and hit one of the stilages with a loud bang, enraging Sid. Another Sid was one of two workers fitting flywheels; most folks steered well clear of this Sid on account of him eating a whole raw onion for lunch each day.
The pistons and conrods (minus the big-end caps) were inserted into the barrels using ring compressors. Care always had to be taken when fitting the big-end cap not to attempt to “wallop” the oil dipper (particularly the hollow dipper on the twins) with the palm of the hand to get it on to the big-end bolts!
If correctly dated to the 1970’s, most engines were probably destined for Iran, where compression change-over valves were still being specified for the single cylinder engines to aid starting in the winter in the mountainous regions. Additionally many engines went to the tropical zones; the slow speed engines were regarded as “Africa-proof” on account of their simplicity and robustness. The sheer weight of a complete genset or pumpset with a cast iron base plate was substantial, yet in the developing world many units were shifted by oxcart or muscle power alone. As smaller engine power outputs increased and weight was reduced, there was some reluctance to change in many countries, as lighter engines were considered at risk of being carried off!
A variety of cooling arrangements were offered, with the most expensive being radiator cooled. Most engines were ordered for tank cooling, or for a feed of cooling water taken from the pump if the engine was made up into a pump-set. Such pump-bleed water could be very cold: in Saudi Arabia, Blackstones sold many replacement cylinder heads for their horizontal engines because of a Arab belief that one must always be able to put a hand on the water outlet from the cylinder block! CS engines with substantial flywheels were easily started by hand – from either end if the ratchet pawl in the starting handle was suitably rotated. With no guards and a heavy cast iron starting handle, it was vital to speedily withdraw the handle off the crankshaft as the engine started up. On one occasion overseas I came to the rescue when a flailing handle still on the shaft of an engine run up to speed threatened to fly off. The stopping control and decompressor were too dangerous to reach, so I took a long length of timber batten, and slowly slid it tangentially to interrupt the handle in the ratcheting mode.
Testing of the slow speed engines was as far as I can recall done using direct-coupled gimballed dc. generators so that a resistive load could be applied, and the torque measured with a balance attached to an arm. The DC generators also acted as starters. The Lister Test Specifications detailed no-load running, quarter load, half load and full load times, after which the engine was passed off as fit to take full load indefinitely – effectively fully run-in. The duration of the test was such that the Test Section always worked a night shift. One “hen-pecked” night tester managed to run a dairy farm during the day.
A minor disaster struck me one freezing morning. There was to be some high-level visit and gen-sets had to be on test; a set needed filling with several gallons of oil, which was very reluctant to flow out of the drum tap. I left it for a few minutes, then returned to find that the 15kW space heater had speeded things up somewhat and at least a gallon had overflowed on to the floor. I grabbed a bag of sawdust and a roll of corrugated paper and carpeted the floor several times, rushed on with the oil fill and startup, and the VIPs were none the wiser.
Before the days of Health and Safety Regulations affecting every aspect of industrial activity, noise levels in factories were largely unregulated. So machine shops, assembly lines and test shops were often extremely noisy. How then did one attract the attention of a passing “dolly-bird” secretary taking paperwork to the foreman’s office? Simple, remove the rocker cover from a running 8/1 diesel engine, and hit the inlet valve rocker end with a mallet – the “CRACK” as the compression is released is dramatic! (This trick is best performed without the oil bath air cleaner being in place, otherwise oil will go everywhere).
One had to be constantly on the look-out for suited passers-by who might represent unidentified authority: whilst Ralph Mumford (our own GM) could be expected to pass by at least once a day, managers from other RAL Works often sniffed around. There were power struggles and empire building going on at that time, as Hawker Siddeley were massively restructuring the entire Diesel Engine Division, from 5hp to more than 10,000hp. We occasionally saw Frank Blackstone (a director of RAL and Lister Blackstone) in bowler hat and pin-stripe suit walking purposefully around apparently for exercise – possibly on “gardening leave”?
Whilst at Cinderford I took an interest in the duties of the Time and Motion engineer, and in how balanced work stages were determined for the assembly track. This was to be very useful to me when subsequently I had to prepare such schedules for 8/1, LR1, SR1-2-3, ST1-2-3, LT1, and HR2-3-4-6 for overseas assembly operations.
In mid-May I had to leave RAL Cinderford to re-take my NCAE exams. Wishing me luck, Ralph Mumford confidentially guaranteed me a job with RAL, pass or fail the exams! I passed and duly completed the final year, and graduated with a BSc Ag. Eng. When I rejoined RAL, I found that Ralph Mumford had been ousted in a management dispute, but he had earlier communicated his offer to Dursley, so I was safe. (Many years later, when along with many former RAL Cinderford colleagues I attended Ralph’s funeral – he was given a rousing send off as a mark of our appreciation and respect).
I had found work at RAL Cinderford very satisfying, as one was trained for the job, then allowed to get on with it. Work colleagues and local management were ever-supportive and subsequently always interested in my career’s progress. A great shame that the RAL Cinderford operation was of the early casualties of many.
The author wishes to assert his copyright: R.A.Davis, January 2017
If you have a Lister Petter story, we’d love to hear from you. Share it with us via enquiry@listerpetter.com.