EMPRESA
NOTICIAS
Todas las novedades se compartirán con usted aquí
R. A. Lister Petter - una mirada personal al pasado
Entré a trabajar en R.A.Lister & Co. Ltd. por casualidad en 1969. Había cometido el pecado capital de suspender un examen de repetición al final de mi segundo año de carrera en el National College of Agricultural Engineering, en Silsoe, y deseaba pasar el "tiempo muerto" obligatorio en un empleo remunerado hasta repetir los exámenes. Al vivir cerca de Ross-on-Wye, la fábrica de RAL en Cinderford estaba a unos treinta minutos en coche de casa. Decidí visitar la fábrica para probar suerte con el Departamento de Personal. No llegué más lejos que la Gate House en Barleycorn Road, donde me rechazó el Gate Man...
"¡No aceptamos trabajadores temporales!"
Sin desanimarme en absoluto, volví a casa, llamé a Personal y me invitaron a entrevistarme con el Sr. Ralph Mumford, el director general, esa misma tarde. Al llegar a la puerta de entrada, el iracundo portero me dijo
"¿Creí que te había dicho que te fueras?"
"¡Lo hiciste, pero tengo una entrevista con el Sr. Mumford a las 2.30!"
La entrevista fue muy favorable y me ofrecieron un puesto de ayudante de probador de grupos electrógenos en la recién creada Sección de Montaje de Grupos Electrógenos, que empezaría en dos semanas. Ralph Mumford se interesó por mi empleo hasta que llegó el momento de retomar mis estudios interrumpidos. (Más tarde me enteré de que el hombre de la puerta era el suegro del director general).
RAL Cinderford fabricaba y ensamblaba la gama de motores Lister de baja velocidad CS, y también producía muchos componentes para Dursley y Swindon. La sección de montaje de grupos electrógenos trabajaba con los motores LR 1-2 y SR1-2-3 producidos en Swindon, junto con algunos motores 8/1, 16/2 y VA, que se acoplaban con alternadores BKB, EEC o Brush. Los paneles de control a medida se fabricaban en la empresa.
(De paso, el VA era efectivamente una versión monocilíndrica refrigerada por aire del 8/1, con diferente sincronización, bmep y sfc - ¡algo ruidoso!)
La fábrica de RAL en Cinderford empleó a muchos mineros desplazados de la cuenca carbonífera de Forest of Dean, que habían soportado grandes dificultades y salarios muy bajos. Los antiguos electricistas de mina, altamente cualificados, encontraron un buen empleo cuando RAL trasladó la producción de grupos electrógenos SR de Walkden o Swindon a Cinderford, complementando los grupos electrógenos 8/1 y 16/2 existentes (más los muy ocasionales VA).
Una vez familiarizado con el equipo y entrenado en los motores y el equipamiento, me dediqué a las tareas de recibir los grupos electrógenos construidos y los paneles de control separados, cablear los dos juntos y conectarlos a los bancos de carga, conectar el escape, las baterías y el suministro de combustible. Todos los motores habían sido probados previamente y estaban listos para la carga completa, pero todos los componentes del panel cableado estaban sin ajustar. Pasé de probar conjuntos simples de carga de baterías a monofásicos y trifásicos autónomos, luego a Start-O-Matic, fallo marginal de la red, doble stand-by, auto-standby a la red, conjuntos auxiliares marinos y conjuntos de larga duración.
Una de las primeras tareas fue ajustar un montón de relés del panel de control (siendo esto antes de la era de la electrónica de estado sólido) con un Variac y un medidor AVO. Me hice un pequeño taburete para facilitar el trabajo en algunos de los paneles demasiado grandes para montarlos en la pared, ya que los ajustes llevaban mucho tiempo en los conjuntos más complejos, y solían tardar medio día si había alguna característica novedosa en el cableado que pillaba desprevenida a la Sección de Paneles. A continuación, había que ajustar los controles del motor: los interruptores de baja presión del aceite y de alta temperatura del aire. A continuación, se podía arrancar el motor (y controlar la secuencia lógica en el caso de los motores con Start-O-Matic instalado y sistemas duales), hacer que alcanzara la velocidad y la temperatura de funcionamiento, comprobar las tensiones en vacío y aplicar las cargas resistivas especificadas, así como establecer los índices de carga de la batería. Si todo iba bien, se supervisaba el procedimiento de apagado; en el caso de los conjuntos dobles, el arranque del segundo conjunto debía supervisarse de forma similar, y entonces se aplicaba la prueba completa. Ninguno de los conjuntos estaba preparado para funcionar en paralelo.
Por regla general, los alternadores instalados eran Brush o BKB (estos últimos, fabricados por Bulpitt, Kent y Bulpitt de Birmingham, estaban siendo eliminados a medida que se imponía la política de compras internas del Grupo Hawker Siddeley). Antes, los alternadores y generadores eran fabricados por Mawdsleys de Dursley.
Para la mayoría de los clientes, las pruebas realizadas por el RAL eran prueba suficiente del rendimiento. Sin embargo, los clientes institucionales, normalmente Lloyds, Crown Agents, Westinghouse y Philips con sistemas críticos a prueba de fallos, enviaban invariablemente a sus propios inspectores para que observaran las "pruebas presenciales". Progresivamente, me tocó a mí realizar dichas pruebas, de mayor o menor complejidad, incluyendo los primeros grupos electrógenos SR1 de doble reserva y largo funcionamiento, descalificados para la gran altitud, para los nuevos enlaces telefónicos de microondas de África Oriental que estaba instalando Philips bv. Algunos de los grupos de Lloyds eran unidades auxiliares marinas que incorporaban una mezcla de alternador, compresor de aire y bomba de incendio/debilge. (No se utilizaban todos al mismo tiempo: los embragues de entrada y salida y los interruptores de bloqueo permitían seleccionar algunas funciones). Los pedidos de Crown Agents incluían algunos grupos electrógenos para aeropuertos dispuestos para una doble reserva a la red eléctrica, reduciendo progresivamente la potencia de forma que el grupo electrógeno final sólo alimentaba las radiobalizas y los rudimentos del control del tráfico aéreo.
En los seis meses que estuve en la Sección de Montaje de Grupos Electrógenos, nunca tuvimos un solo fallo en las pruebas. Sin embargo, condené un palé entero de reguladores Lucas, y tuve que instruir a la Sección de Paneles en la importancia de observar la polaridad de los diodos de alta corriente (su primer dispositivo de estado sólido, introducido en 1969 para los conjuntos de carga de baterías SR1).
Teniendo en cuenta que la más compleja de las combinaciones incluía dos paneles de interruptores del tamaño de un pequeño armario, las respectivas secciones realizaron algunas hazañas notables trabajando a "distancia" del equipo de diseño. Sólo en una ocasión tuvimos que llamar al jefe de diseño eléctrico de Dursley para que interpretara la secuencia lógica de las especificaciones. Recuerdo muy bien el suceso, ya que Harry Taylor llegó justo cuando yo estaba a punto de salir: Gané un extra de 5/- por el corto periodo de horas extras resultante, pero pagué 7/6d más en impuestos esa semana, (¡habiendo cruzado el umbral de impuestos!).
Mis funciones nunca se definieron con claridad, ya que en realidad estaba a prueba, al ser la persona con mejor formación técnica de la Sección de Montaje de Conjuntos. Sólo dos meses después de ser contratado, mi capataz, Ray, estuvo de baja por enfermedad tras una operación de hernia. Pronto me encontré con que tenía que ocuparme de problemas administrativos y técnicos que los otros capataces eran reacios a asumir, y aprendí mucho sobre la gestión.
El mercado de los grupos electrógenos estaba en plena efervescencia, lo que provocó una gran actividad: esto, unido a una época de auge en la producción de motores de baja velocidad, hizo que todo el mundo estuviera de enhorabuena a principios de 1969.
- Una semana de cinco días
- Horas extras tres tardes a la semana (lunes, martes y jueves)
- Media jornada los sábados
- Todo el día los domingos
Y ni una sola queja. Mi sueldo como probador de grupos electrógenos (con horas extraordinarias y bonificaciones, antes de impuestos pero después de deducir los gastos generales semanales del azul, la contribución al seguro social, etc.) era de 25 libras esterlinas a la semana. Los impuestos se recuperaron una vez que volví a mis estudios.
Mientras dedicaba la mayor parte de mi tiempo a mis tareas de comprobación, aprovechaba cualquier oportunidad para observar lo que hacía la fábrica y cómo se gestionaba. Se fabricaba una amplia gama de piezas de motor y de otro tipo en máquinas-herramienta comunes a todos los trabajos de ingeniería: capstans Ward, bar autos, taladradoras multihusillo, rectificadoras Jackman, etc., con algunos leviatanes más específicos, como los tornos verticales Bullards y Webster y Bennet para el mecanizado de los volantes gemelos que caracterizaban la gama de motores de baja velocidad. El orgullo de la exposición fue la taladradora de plantilla SocieteˊGenevoise para el cuarto de herramientas. También se fabricaban otros componentes y equipos no relacionados con el motor, principalmente maquinaria agrícola para la empresa asociada Lister Agriculture. La unidad de extracción de humedad de Lister (montada en un patín o en un remolque) para el secado de las cosechas y los dos modelos de prensas de granulación de piensos se fabricaban en parte y se montaban y probaban en Cinderford, compitiendo a menudo por los escasos recursos de mano de obra y maquinaria.
La sección de montaje de grupos electrógenos ocupaba parte de una nave típica de una fábrica del tipo North-Light, construida en parte con materiales sobrantes del Gobierno en los años de la posguerra, incluso de un hangar de aviones de la época de la guerra en Windsor Great Park que se había construido allí por si la Familia Real se veía obligada a huir del país. Las columnas de acero que soportaban los puentes grúa habían formado parte del Mulberry Harbour. La nave se compartía con la Sección de Embalaje, y estaba junto a las naves de ensamblaje y prueba de motores de baja velocidad. Los almacenes de piezas se encontraban entre la fabricación de componentes y las vías, y las células de submontaje se alimentaban de las vías en los puntos adecuados.
Como los componentes del motor de baja velocidad eran de diseño relativamente antiguo, era interesante ver cómo se perpetuaban las técnicas de fabricación anteriores. Es típico el montaje del árbol de levas, en el que las levas individuales se calentaban, se prensaban y se clavaban en un eje liso. El piñón del cigüeñal se calentaba tradicionalmente en una plancha de gas antes de ser conducido rápidamente; sólo a mediados de 1969 se introdujo un calentador de inducción. Muchos de los componentes eran pesados y requerían fuerza muscular para manipularlos. Aunque se utilizaban polipastos de aire para levantar los volantes, colocarlos en el cigüeñal paralelo y montar las chavetas era un trabajo duro, que a veces requería varios ajustes si el agujero del volante era estrecho.
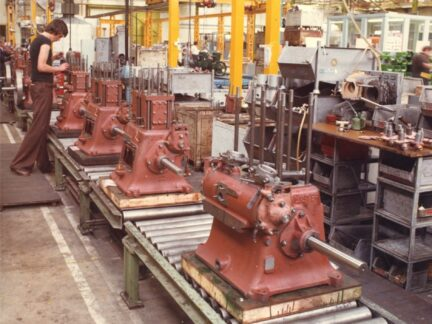
En la imagen de la cadena de montaje de Cinderford se ve un lote de motores 16/2 en marcha. Desgraciadamente, no se muestra ningún polipasto para levantar los cilindros por separado, lo que superaría con creces la capacidad del muchacho que se muestra. ¿Dónde ha ido el resto del equipo? Sin duda, apartados en aras de la claridad.
La orientación de la vía y otras características de la Sección de Montaje, tal como se muestra, difieren de las que prevalecían en 1969, cuando yo trabajaba en el montaje y prueba del grupo electrógeno adyacente; además, todo es más ligero y menos dickensiano. La cabina de pintura original (una Andrea Filter Back) puede haber sido sustituida, ya que el medio filtrante de tipo papel era propenso a incendiarse. Lamentablemente, no se muestran las operaciones de submontaje, que siempre eran periféricas a la vía para introducir los componentes ensamblados en la fase correcta, con los operarios realizando varias tareas.
En 1969, había un almacén de piezas con grandes zancos (atendidos por "Herman Sid") a la derecha de la pista: un truco favorito era lanzar una gran tuerca Whitworth al otro lado de la tienda desde la sección de montaje de grupos electrógenos, a la izquierda, y golpear uno de los zancos con un fuerte golpe, enfureciendo a Sid. Otro Sid era uno de los dos trabajadores que montaban volantes; la mayoría de la gente se mantenía alejada de este Sid porque se comía una cebolla cruda entera cada día.
Los pistones y las bielas (menos los casquillos de la culata) se introducían en los barriles con compresores de anillos. Al colocar la tapa del cilindro, siempre había que tener cuidado de no intentar "golpear" el cazo de aceite (especialmente el cazo hueco de los gemelos) con la palma de la mano para colocarlo en los tornillos del cilindro.
Si la fecha correcta es la de los años 70, la mayoría de los motores se destinaban probablemente a Irán, donde todavía se especificaban válvulas de cambio de compresión para los motores monocilíndricos con el fin de facilitar el arranque en invierno en las regiones montañosas. Además, muchos motores se destinaron a las zonas tropicales; los motores de baja velocidad se consideraban "a prueba de África" debido a su simplicidad y robustez. El peso de un grupo electrógeno completo o de un grupo de bombeo con una placa base de hierro fundido era considerable, pero en el mundo en desarrollo muchas unidades se desplazaban sólo con carretas o con fuerza muscular. A medida que aumentaban las potencias de los motores más pequeños y se reducía su peso, en muchos países había cierta reticencia al cambio, ya que se consideraba que los motores más ligeros corrían el riesgo de ser arrastrados.
Se ofrecía una variedad de sistemas de refrigeración, siendo el más caro el refrigerado por radiador. La mayoría de los motores se pedían con refrigeración por depósito, o con una alimentación de agua de refrigeración tomada de la bomba, si el motor estaba constituido en un conjunto de bombas. El agua de la bomba podía estar muy fría: en Arabia Saudí, Blackstones vendió muchas culatas de repuesto para sus motores horizontales debido a la creencia árabe de que ¡siempre hay que poder poner una mano en la salida de agua del bloque de cilindros! Los motores CS con volantes de inercia importantes se arrancaban fácilmente a mano, desde cualquier extremo, si se giraba adecuadamente el trinquete de la manivela de arranque. Sin protectores y con una pesada manivela de arranque de hierro fundido, era vital retirar rápidamente la manivela del cigüeñal cuando el motor arrancaba. En una ocasión, en el extranjero, acudí al rescate cuando una manivela agitada que seguía en el eje de un motor en marcha amenazaba con salir volando. El mando de parada y el descompresor eran demasiado peligrosos para alcanzarlos, así que cogí un largo listón de madera y lo deslicé lentamente de forma tangencial para interrumpir la manivela en el modo de trinquete.
Las pruebas de los motores de baja velocidad se realizaban, por lo que recuerdo, con generadores de corriente continua acoplados directamente, de modo que se podía aplicar una carga resistiva y medir el par con una balanza sujeta a un brazo. Los generadores de CC también actuaban como arrancadores. Las especificaciones de la prueba Lister detallaban los tiempos de funcionamiento en vacío, a un cuarto de carga, a media carga y a plena carga, tras lo cual el motor se consideraba apto para soportar la carga completa de forma indefinida, es decir, totalmente rodado. La duración de la prueba era tal que la Sección de Pruebas siempre trabajaba en turno de noche. Uno de los probadores nocturnos "pechugones" se las arreglaba para dirigir una granja lechera durante el día.
Una mañana gélida me ocurrió un pequeño desastre. Había que hacer una visita de alto nivel y los grupos electrógenos tenían que estar en prueba; había que llenar un grupo con varios galones de aceite, que se resistía a salir del grifo del bidón. Lo dejé durante unos minutos y volví para descubrir que el calentador de 15kW había acelerado un poco las cosas y que al menos un galón había rebosado en el suelo. Cogí una bolsa de serrín y un rollo de papel corrugado y alfombré el suelo varias veces, me apresuré a llenar de aceite y a ponerlo en marcha, y los VIP no se dieron cuenta.
Antes de que existieran las normativas de salud y seguridad que afectaban a todos los aspectos de la actividad industrial, los niveles de ruido en las fábricas no estaban regulados en su mayor parte. Por ello, los talleres de maquinaria, las cadenas de montaje y los talleres de pruebas solían ser extremadamente ruidosos. Entonces, ¿cómo se podía atraer la atención de una secretaria que pasaba por allí para llevar el papeleo a la oficina del capataz? Muy sencillo, se quitaba la tapa de balancines de un motor diésel 8/1 en funcionamiento y se golpeaba el extremo del balancín de la válvula de entrada con un mazo: ¡el "CRACK" al liberar la compresión es espectacular! (Este truco se realiza mejor sin que el filtro de aire en baño de aceite esté en su lugar, de lo contrario el aceite irá por todas partes).
Había que estar siempre atento a los transeúntes trajeados que pudieran representar una autoridad no identificada: mientras que Ralph Mumford (nuestro propio director general) podía pasar por lo menos una vez al día, los directores de otras fábricas de RAL solían husmear. Había luchas de poder y construcción de un imperio en esa época, ya que Hawker Siddeley estaba reestructurando masivamente toda la División de Motores Diesel, de 5hp a más de 10.000hp. De vez en cuando veíamos a Frank Blackstone (director de RAL y Lister Blackstone) con bombín y traje a rayas, caminando decididamente, aparentemente para hacer ejercicio, ¿posiblemente de "permiso de jardinería"?
Durante mi estancia en Cinderford me interesé por las tareas del ingeniero de tiempo y movimiento, y por cómo se determinaban las etapas de trabajo equilibradas para la pista de montaje. Esto me resultó muy útil cuando, posteriormente, tuve que preparar dichos calendarios para el 8/1, LR1, SR1-2-3, ST1-2-3, LT1 y HR2-3-4-6 para las operaciones de montaje en el extranjero.
A mediados de mayo tuve que dejar el RAL de Cinderford para volver a hacer los exámenes del NCAE. Deseándome suerte, Ralph Mumford me garantizó confidencialmente un trabajo en la RAL, ¡pasara o no los exámenes! Aprobé y completé el último año, y me gradué con un BSc Ag. Eng. Cuando me reincorporé a la RAL, descubrí que Ralph Mumford había sido destituido en una disputa de la dirección, pero había comunicado antes su oferta a Dursley, así que estaba a salvo. (Muchos años más tarde, cuando junto con muchos antiguos colegas de RAL Cinderford asistí al funeral de Ralph, se le despidió de forma entusiasta como muestra de nuestro aprecio y respeto).
El trabajo en RAL Cinderford me resultaba muy satisfactorio, ya que uno recibía formación para el trabajo y luego se le permitía seguir adelante con él. Los compañeros de trabajo y la dirección local siempre me apoyaron y posteriormente siempre se interesaron por el progreso de mi carrera. Es una pena que la operación de RAL Cinderford fuera una de las primeras víctimas de muchas.
El autor desea hacer valer sus derechos de autor: R.A.Davis, enero de 2017
Si tiene una historia de Lister Petter, nos encantaría conocerla. Compártela con nosotros a través de enquiry@listerpetter.com.